Cracking Ammonia: panel wrap-up from the Ammonia Energy Conference
By Julian Atchison on February 19, 2021
When should we be cracking ammonia? How much should we be cracking? How could better cracking technologies open up new end uses? What are the critical challenges still to be overcome for cracking ammonia?
On November 17, 2020, the Ammonia Energy Association (AEA) hosted a panel discussion moderated by Bill David from Science and Technology Facilities Council (STFC), as well as panel members Josh Makepeace from the University of Birmingham, Joe Beach from Starfire Energy, Gennadi Finkelshtain from GenCell Energy, Camel Makhloufi from ENGIE, and Michael Dolan from Fortescue as part of the recent Ammonia Energy Conference. All panelists agreed that cracking technology as it stands has a number of key areas that need to be optimised, particularly catalysts and energy efficiency. But successful demonstrations of modular, targeted cracking solutions are accelerating the conversation.
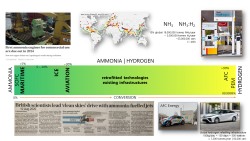
For Bill David, ammonia will become a dominant presence in international transportation and storage of low-carbon alternative fuels. Cracking technologies open up the full suite of fuel cell applications, from pure ammonia SOFCs to ultra-pure hydrogen PEM fuel cells. Up until now, hydrogen production for vehicle transport has always been “just in time”, but cracking solutions and plentiful stocks of low-carbon ammonia could remove that bottleneck. The question is, what stage of maturity are these cracking solutions at currently? Ambition is great, but what demonstration projects are currently showing the most promise out in the field?
Critical challenges
Josh Makepeace pointed out that limitations remain for ammonia cracking technologies as they are currently developed. Technology maturity and “plug and play” assumptions are unhelpful, as key challenges have yet to be overcome before we see affordable, off-the-shelf cracking units appear. A review of the current status of cracking technologies — including techno-economic considerations — is a focus for Josh and the AEA’s Cracking Ammonia Working Group.
One critical challenge — touched on by multiple panelists — is catalyst evolution. Bill and Josh’s research into catalyst optimization is promising, and there’s hope that alkali amide-based catalysts will overtake expensive, supply-limited Ruthenium catalysts to become the next generation. The current generation of nickel-based catalysts only runs at 30-60% electrical efficiency and produces product streams with high residual ammonia (<30ppm) and nitrogen (up to 25%). High temperatures are also required to achieve full cracking in Ni-based units, making them unsuitable for a wide range of applications. But, at 1500kg/day potential hydrogen output, Ni-based heterogeneous cracking does show promise for scalability. Rather than relying on the development of a universal solution, Josh believes the trick will be striking a balance between purity, efficiency and cost for each individual application.
Cracking ammonia for power generation
We then heard from the perspective of four end-use applications. Agreeing with the general sentiment that cracking should be minimised where possible, Joe Beach reported on Starfire Energy’s successful demonstration of burning a 70%-30% ammonia-cracked ammonia fuel blend in a commercial 44kW gas burner. Starfire’s upstream cracking unit produced a product stream suitable for combustion applications through the utilisation of a Cobalt-based catalyst (avoiding the need to use Ruthenium) and overall the system resulted in NOx emissions either below regulatory limits or low enough to be treated with selective catalytic reduction. The results fit in nicely to a suite of studies concerning ammonia combustion in ICE engines, where the 70%:30% blend seems to give the lowest NOx emissions and ammonia slip while delivering stable power output. Paired with additional Starfire and partner technologies, the cracking unit is capable of producing 99.999%, >700bar hydrogen.
The next challenge for Joe and Starfire Energy is to capture waste heat to power the cracker. Conventional gas turbines only work at 40% efficiency: 2.5 MW of fuel energy is required to get 1 MW of power generation out. That 1.5 MW waste heat gap presents an opportunity, as only 0.2 MW is needed to power Starfire’s cracking unit. The possibility of being able to run gas turbines on blended ammonia fuels without having to de-rate the power output is an exciting prospect – once the energy efficiency of the setup is improved.
Gennadi Finkelshtain then presented GenCell Energy’s off-grid, modular, power generating A5 system. The A5 is powered by liquid ammonia, with a small cracking unit feeding into an alkaline fuel cell that generates power at <25 Euro cents/kWh – lower than the price of diesel-generated electricity. The next challenge is — similar to Starfire Energy’s — to capture and utlise waste heat to drive that power generation cost below 15 Euro cents/kWh, achieving grid parity with the EU. Gennadi is certain that robust, modular power-generation solutions like these are “running, not walking” towards commercialisation, and will be able to displace diesel-powered modules in off-grid settings.
Marine on-board cracking
For marine settings, Camel Makhloufi from ENGIE reported on his team’s promising research into on-board power generation. Ammonia and hydrogen fuel blends show the most promise for marine engines, so some level of on-board cracking is desired. But, with their variable load, marine engines are an inappropriate power source for the cracker. This problem might be overcome by the use of autothermal reformers that capture exhaust gas heat to power cracking units, but therein lies another issue – these exhaust gases aren’t hot enough for conventional, Ni-based cracking units.
To achieve full cracking at lower temperatures (around 400°C), ENGIE has successfully demonstrated a new advanced membrane reactor technology, which applies a vacuum to the reactor permeate. An open access technical paper describing this work, H2 production via ammonia decomposition in a catalytic membrane reactor, was published this week in the journal Fuel Processing Technology.
Cracking for fuel cell vehicles
Michael Dolan closed the speaker presentations with an overview of Fortescue’s plans to use hydrogen and ammonia to power its vehicle fleet. While ammonia is the preferred fuel for heavy rail and shipping transport, PEM fuel cells will be necessary for road transport – and this means cracking will be required. Though there are obvious purification challenges associated with hydrogen for vehicle fuel cells, an existing partnership with CSIRO shows promise. Working with CSIRO (and supported by an MoU with Hyundai), Fortescue intends to scale up CSIRO’s patented metal membrane cracking technology from 10kg/day to 200kg/day output – about the right amount for vehicle refuelling. Energy efficiency problems remain, but — as shown by Camel and ENGIE — there are opportunities to apply systems thinking to repurpose waste heat and by-products to optimise the overall process. Ultimately, Michael wants to see containerised, turn-key, safe ammonia cracking solutions mass-produced and be available to plug into any source of ammonia around the world.
If you wish to view the archived video of the cracking ammonia panel discussion, please register for the conference to access all session recordings. You can also browse and download all of the Ammonia Energy Conference 2020 presentations.
*This article has been updated after advice from Starfire Energy.