EverWind Fuels: first-to-market ammonia exports from Canada’s Maritime provinces
By Kevin Rouwenhorst on February 20, 2025
In our February episode of Project Features, Brendan Chard from EverWind Fuels and Michael Goff from Black & Veatch discussed wind-based renewable ammonia production in Nova Scotia and lessons learned from the recently-finished FEED study for the Point Tupper project. The recording is available on the AEA’s website, and you can also download the speaker presentations.
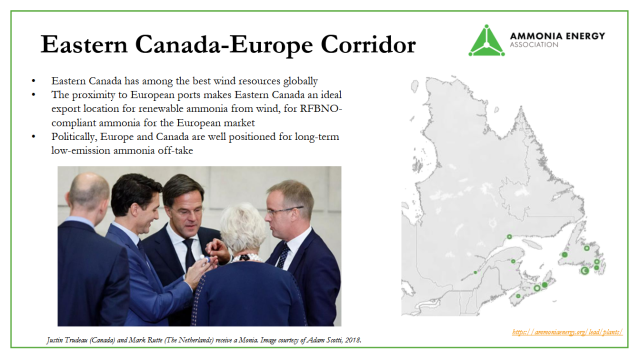
Click to enlarge. Discussions on an Eastern Canada-Europe ammonia supply corridor began in the 2010s. From Kevin Rouwenhorst, February 2025 Project Features introduction.
Canada’s eastern coast has some of the best wind potential globally. Various renewable ammonia projects have been announced on Canada’s eastern coast, with a focus on exporting the product to Europe. The distance between Eastern Canada and Northern Europe is about half that of the distance between the US Gulf Coast and Northern Europe, decreasing transport costs.
Discussions regarding an Eastern Canada-Europe corridor for renewable hydrogen and ammonia were initiated in the late 2010s. Canada and Europe are long-term political allies, making Canada well positioned for long-term ammonia supply to Europe. Also, the German and Canadian governments have announced a joint auction via the H2Global mechanism, with a combined funding of around €400 million for RFNBO-compliant ammonia supply to Europe.
The Point Tupper Project
EverWind Fuels is developing various projects in Eastern Canada, including the Point Tupper project in Nova Scotia. Point Tupper is the deepest ice-free port on the East Coast of Canada, and features an existing terminal site with a skilled workforce and freshwater availability.
The first phase of the Point Tupper project features 240,000 tons per year of ammonia production, aiming for first operations in 2026. The project is connected to the grid, with 800 MW of new renewable development for electricity supply, including 650 MW of wind, 150 MW of solar PV, and 50 MW/100 MWh of battery energy storage systems (BESS). Environmental approval is already in place for various wind farms and for the renewable ammonia production facility itself, while also the FEED work has been completed. The projects are developed in cooperation with First Nations communities.
The project is finalizing electrolyzer and ammonia loop technology selection, and expects a capacity of up to 750 metric tons per day. The Point Tupper project has been pre-certified by CertifHy, and produced ammonia will be compliant with RFNBO requirements for imports into Europe.
In early 2025, EverWind Fuels completed its Canadian Clean Hydrogen Investment Tax Credit (ITC) submission, claiming a 99% emission reduction versus fossil-based ammonia production, allowing for the highest tier of tax credits at 40%. Various MoUs are also in place for ammonia offtake, which are set to be finalized in 2025 for EverWind Fuels to reach FID on the project.
Click to enlarge. Details of the first phase of the Point Tupper project. From Brendan Chard, Atlantic Canada’s Premier Green Fuels Hub (Feb 2025).
All coal-fired power plants must be retired in Nova Scotia by 2030, and 80% of electricity must come from renewables. While the Point Tupper project is initially focused on export to Europe, local grid stabilization services in Nova Scotia can be provided by flexible operations at the ammonia plant, and even the use of ammonia as peaker fuel for power generation. FEED work confirmed that the electrolyzers will be able to be turned down to zero load, and the ammonia plant can turn down to its minimum power requirement of around 15 MW from the grid, both within 10 minutes notice.
EverWind Fuels also has other ammonia projects in Eastern Canada, aiming to become a multi-site interconnected hub. A second phase of the project in Nova Scotia could see up to 3 GW of wind and solar PV capacity, combined with transmission infrastructure, for an annual production volume in excess of 1 million tons of ammonia. Another project on the Burin Peninsula in the province of Newfoundland & Labrador could produce in excess of 3.4 million tons of ammonia each year from 12 GW of wind and solar PV capacity, in multiple phases. Lastly, offshore wind may be utilized, once the cost of offshore wind electricity decreases sufficiently.
Lessons learned from designing flexible ammonia production
The FEED work for the Point Tupper project was completed by Black & Veatch, an engineering consultant and engineering, procurement & construction (EPC) company, with about 110 year history in infrastructure and decades of experience in ammonia plants. Black & Veatch has commissioned or is building a total of 365 MW of electrolysis capacity.
The Point Tupper design relies on credible renewable electricity profiles on an hourly resolution, to size and optimize the downstream processes. Typically, the air separation unit (ASU) needs to be operated continuously, with a liquid nitrogen storage to account for fluctuating nitrogen demand from the ammonia synthesis plant. The electrolyzers for hydrogen production are much more flexible, with ramping from zero to 100% within a matter of minutes, and stacks can be shut down individually to allow for a higher overall flexible load for the hydrogen plant. Hydrogen production accounts for around 90% of the energy consumption of an ammonia plant, implying that its ability to follow renewable profiles is key.
The ammonia synthesis plant will be relatively flexible, able to be ramped between 10% load and nameplate capacity, with a ramp rate of about 1-3% per minute. However, it should be noted that a 10% load in terms of ammonia production would still require the compressors to operate at around 70% of the nominal load, meaning that the relative energy consumption of the ammonia plant increases. For this reason the ammonia plant is ideally not turned down completely, and hydrogen storage buffers can be utilized to feed the ammonia plant when renewable electricity supply is absent. Hydrogen storage buffers and battery energy storage systems (BESS) are minimized as much as possible however, as these are expensive backstops.
Click to enlarge. Key lessons from the design of renewable ammonia plants, from Michael Goff Atlantic Canada’s Premier Green Fuels Hub (Feb 2025).
Flexibility brings challenges and complexity to the design. Buffers such as liquid nitrogen storage, pressurized hydrogen storage, and batteries provide operational flexibility. Proper analysis is required for metal fatigue, due to pressure and temperature cycles in the ammonia synthesis plant. Prediction of renewable profiles allows for ramping the ammonia plant accordingly. Due to the different ramp rates and overall flexible range of unit operations, it is best to control each process unit independently with the appropriate storage buffers, rather than ramping up and down all units simultaneously.
Although electrolysis plants have been operated for over a century, electrolysis plants at the required scale and with flexible operation are relatively new. Performance of the plant over long time frames and flexible operating conditions will be a key learning point of the project. To help guarantee this long-term performance, use of credible vendors with an industrial track record is key.
Furthermore, codes and standards for large-scale electrolyzer plants with hundreds of MWs of electricity entering an electrolyzer building for hydrogen and oxygen production (and heat production) are still developing, including the implementation of the codes to design for safe operation is a new challenge. Leak detection of hydrogen needs to be addressed, as hydrogen build-up and leaks in general cause a safety hazard. Also, the electrolyzers generate significant heat, implying that an appropriate design for the water cooling system is important as well.
One last lesson learned from the FEED study concerns modularization. Currently, there is a shortage of construction capability, implying significant cost uncertainty for on-site construction. Modularization allows for minimal construction on-site and a higher cost certainty. Modularization is well suited for projects with the size of the first phase of the Point Tupper project, although it may be less applicable for world-scale ammonia plants.