8 Rivers in Texas: deploying 8RH2 technology for carbon capture beyond 99%
By Kevin Rouwenhorst on May 23, 2024
In our April episode of Project Features, Steve Milward and Maulik Shelat from 8 Rivers joined us to discuss their 8RH2 technology for gas-based hydrogen production with carbon capture rates beyond 99%. The technology will be deployed at Cormorant Clean Energy in Texas, the first ammonia production project based on 8RH2. The recording is available on the AEA’s website, and you can also download the speaker presentations for more details.
Background
In conventional hydrogen production, about two-thirds of the CO2 from a steam methane reformer is easily captured from process gas. The last third of the CO2 is produced from burning gas for heat generation, external to the SMR furnace. This dilute CO2 (vented in flue gas) is currently not captured, due to the high cost.
Higher carbon capture rates are possible using autothermal reforming (ATR) technology, with carbon capture rates around 95%, according to IRENA. However, this still leaves around 5% of residual CO2 emissions. As a potential solution to this, 8 Rivers has developed the 8RH2 technology for hydrogen production, which aims at carbon capture rates beyond 99%.
The Allam-Fetvedt cycle
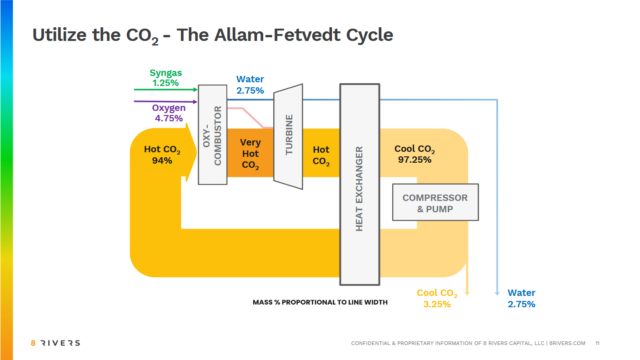
Click to expand. The Allam-Fetvedt cycle, which sits at the core of 8 Rivers’ technology development. From Steve Milward and Maulik Shelat, From Problem to Solution: How CO2 Enables Affordable Clean Hydrogen (Apr 2024).
8 Rivers is a company focused on CO2 capture, and bringing low TRL (technology readiness level) technologies toward commercialization via industrial R&D and implementation. Technology development examples include Biome (the biomass variant of the Allam-Fetvedt cycle), 8RH2 (gas-based hydrogen production with CO2 capture rates >99%), calcite (Direct air capture of CO2), and TarT (H2S removal from gas). 8 Rivers also founded NET Power in 2010, which aims to deploy elements of these new technologies for power generation.
The Allam-Fetvedt cycle is at the core of 8 Rivers’ technology development. This process takes a mixture of hydrogen (H2) and carbon monoxide (CO) into an oxycombustor co-fed with purified oxygen (O2). This produces “very hot” CO2 (at 900°C and 300 bar), as well as water and steam. The “very hot” CO2 is used in a turbine to generate electricity. Afterwards, the outlet CO2 is cooled through a heat exchanger, resulting in “cold” CO2 at near-ambient temperatures. The vast bulk of this “cold” CO2 (97.25%) must be conserved, and sent back to the heat exchanger to produce “hot” CO2, restarting the process. But a small part (3.25%) of the “cold” CO2 can be removed (or “tapped off”) from the gas stream. Because this small part can be removed at pressures ranging between 30 and 150 bar, a range of use cases is available, including permanent sequestration. Although this removed CO2 can be purified to food grade levels, that would mean that 45Q tax credits (see below) and certification associated with the produced hydrogen would be foregone.
Thus, the Allam-Vetvedt cycle operates in a semi-closed loop with CO2. As CO2 is the pure working fluid in the Allam-Vetvedt cycle, it does not need to be captured. This is a clear advantage versus SMR and ATR-based setups, where amine solutions are required for CO2 capture.
8RH2 technology
Click to expand. Hydrogen production via 8HR2. From Steve Milward and Maulik Shelat, From Problem to Solution: How CO2 Enables Affordable Clean Hydrogen (Apr 2024).
The Allam-Fetvedt cycle and the oxycombuster are at the core of the 8RH2 technology. Instead of using the “hot” CO2 for running a turbine, it is used as the working fluid for heating reformer tubes, within which hydrogen is produced from methane. No burners are required. This technology is called a CO2 convective reformer (CCR), owing to the convective heat transfer from the “hot” CO2 working fluid toward the reformer tubes. The Nickel-based catalyst and the steam to carbon ratio used within the reformer tubes are the same as for a steam methane reformer. The CCR is a tube-in-tube construction, similar to a counter-current shell and tube heat exchanger featured in modern SMR plants. Casale is a technology partner for scaling up the 8RH2 technology.
Further conversion of gas occurs in a secondary reformer, which can be fed with pure oxygen (or air, to introduce the nitrogen for ammonia synthesis loop). A final conversion step occurs via the water gas shift reaction, with the hydrogen subsequently purified with a PSA (pressure swing adsorber). The off-gas (mainly carbon monoxide) from the PSA is redirected and used in the oxycombustor. In the overall 8RH2 technology setup, the oxycombustor is the main element that needs to be de-risked, with steps currently being taken to do so (8 Rivers expects imminent announcements on that front).
Cormorant Clean Energy, Texas
Click to expand. Details of Cormorant Clean Energy, including key partners. From Steve Milward and Maulik Shelat, From Problem to Solution: How CO2 Enables Affordable Clean Hydrogen (Apr 2024).
8 Rivers’ focus is on large-scale applications for 8RH2, as this is where the economics for low-emission gas-based hydrogen and ammonia production work best. The first project utilizing the 8RH2 technology is Cormorant Clean Energy, which will be located in Port Arthur, Texas (USA). The project has an annual capacity of 880,000 tons of ammonia, which will be primarily exported to the Asian market. About 1.5 million tonnes of CO2 will be captured and sequestered each year.
The 45Q tax credit within the Inflation Reduction Act is targeted for this project (85 USD per tonne CO2 permanently sequestered). Since March 2022, the parties involved in Cormorant Clean Energy have been in contact with the regulatory bodies and policy makers. There has also been early, extensive engagement with the local Port Arthur community. As Steve Milward explains: “the community knew about this project before the public did”. At least 95 permanent jobs will be generated by the project, with more than a thousand jobs during construction, with a focus on local suppliers and labor.
Current activities include permitting, as well as an ongoing FEED study currently being conducted by Fluor, with the aim to conclude before the end of 2024. In parallel, a FEED study is ongoing for an ammonia pipeline from the production facility to a 70,000 ton capacity storage tank at the port. FID for Cormorant Clean Energy is expected by early 2025.
Future scale-up of the technology is foreseen, and will be mainly limited by the size of equipment that can be manufactured. For reference, Cormorant Clean Energy will have an ammonia loop with a capacity around 2,500 tonnes per day, licensed by Casale. Various ammonia licensors have already developed licensed technologies for loop capacities up to 5,000 – 10,000 tons per day.
8 Rivers owns the technology for 8RH2 in the first few projects, to better understand the technology under operating conditions. Afterward, such 8RH2 may be licensed to third parties around the world for further projects.