Methane splitting and turquoise ammonia
By Cedric Philibert on May 14, 2020
A guest article by Cédric Philibert, independent consultant and former Senior Analyst at the International Energy Agency.
Most hydrogen today is produced from fossil fuels – steam methane reforming of natural gas, partial oxidation of coal or oil residues – and entails large CO2 emissions, from 8.5 tons of CO2 per ton of H2 from natural gas in modern facilities up to 20 tCO2/tH2 from coal. This fossil hydrogen can be called “grey hydrogen”. Or sometimes, brown. The same color scheme applies to the ammonia produced from it, so we have “grey ammonia.” Or brown ammonia, your call. The exact carbon footprint depends on the fuel used and the efficiency of the facility, so you could easily identify many shades of grey.
Green is the colour of hydrogen produced from electrolysis of water, provided the process is run on green electricity, which most understand as renewables-based, although some insist nuclear power also qualifies if green means (very) low carbon. Reforming biogas would be green too but, because a significant amount of hydrogen might be used to make sustainable hydrocarbon fuels for, say, aviation, it might in the future be more useful to add hydrogen to biomass than to subtract hydrogen from biomass.
Blue is the colour of hydrogen produced from fossil fuels, but with capture and storage of carbon dioxide (CCS). The International Energy Agency systematically uses the term carbon dioxide capture and use or storage, “CCUS”. But CO2 is both used and stored only in enhanced oil recovery operations. From hydrogen and ammonia production, process CO2 is used in integrated ammonia/urea plant for manufacturing urea from ammonia – and released into the air soon after urea is used in the crops. Most other uses of CO2 involve manufacturing of hydrocarbons, starting with synthetic methane. However, reforming methane into hydrogen and CO2 for then making synthetic methane may not be the most clever thing to do. Let us stick to CCS to qualify for blue hydrogen, though depending on the fuel use, the share of CO2 captured, and the upstream methane emissions from natural gas exploitation, the blue may range from pale to dark, or from, say, sky blue to navy blue.
There is, however, another option to deliver clean hydrogen – and now another colour: turquoise, or green-blue (or blue-green). This is the colour of hydrogen from methane pyrolysis, a process that directly splits methane into hydrogen and solid carbon. Instead of being a waste, like CO2, that must be disposed of safely, solid carbon is potentially a resource, with various industrial uses. To be fair with electrolysis, it has also a valuable by-product, oxygen, absent from methane splitting.
This “Türkiser wasserstoff,” as Robert Schlögl, director of the Max-Plank Institute in Berlin, nicknamed it first, is of great interest in Germany, where storage of gaseous CO2 is rather unpopular. The German Green Party, for example, states that CCS is neither safe, economically sound, nor accepted by the population, and thus rejects blue hydrogen. (Contacted, the Blue Party declined to comment on green hydrogen).
Methane pyrolysis or methane-splitting, is not a new concept. A commercial-scale plant already existed near Montreal, in the Belle Province (Québec) of Canada. A new one is under construction in the Cornhusker State (Nebraska) of the USA. And scientists and engineers are working on it in Australia, Germany, France, the Netherlands, and Russia – a non-exhaustive list.
Natural gas is only a feedstock. All energy for the process comes as electricity, presumably green. The minimum energy required, 38 kJ/mol H2, is much less than for water splitting via electrolysis, 285 kJ/mol H2 or steam methane reforming, 252 kJ/mol H2. Natural gas has an energy potential coming partly from its carbon atom, partly from its four hydrogen atoms. In combustion, all would be oxidised and free energy, turning into CO2 and water. The pyrolysis of methane does not use the potential energy of carbon, which remains unoxidized, but the hydrogen that results has an energy potential originating from the natural gas (plus a fraction of the electricity used). Water as a feedstock, by contrast, has no energy potential, the hydrogen atoms of the H2O molecule being already completely oxidised. All the energy potential of the hydrogen resulting from electrolysis is brought in the electricity that runs the process. In practice, the ratio is less advantageous depending on the pyrolysis technology and the losses that result from the high temperatures needed, but methane splitting still requires 4 to 5 times less electricity than electrolysis.
How does methane pyrolysis work?
Several technology options are competing.
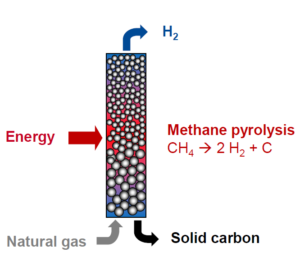
Catalytic thermal decomposition is the most common and is actively pursued in particularly by the German chemist giant BASF. Introduced from the bottom of a vertical reactor, the natural gas is pre-heated in exchanging with carbon particulates on their way out by gravity, then heated at above 800°C by electric induction in the middle of the vertical reactor, while hydrogen escapes from the top. The carbon atoms resulting from the split coagulate and then go down to the bottom of the reactor, progressively growing in size by aggregation and agglomeration before being extracted as carbon particulates of millimetres diameter size.
After years of R&D, BASF is currently building a third pilot, which is the size of a small building.
This temperature level and the use of catalysts usually creates issues relative to the quality of the solid carbon products and to the purity of the hydrogen produced. Carbon particulates of this size can be used in steel making or concrete but have relatively little value, although BASF eyes the more profitable markets of carbon electrodes. One possible use of this process in a large chemical plant with hundreds of different processes and thousands of different products, such as the BASF plant in Ludwigshafen (Germany), might be to produce synthesis gas (a mix of H2 and CO) with a very low CO2 footprint by reacting turquiose hydrogen with an external source of CO2.
In Australia, the Hazer Group based the thermal decomposition of methane on the use of iron ores as catalysts – an abundant and cheap resource. Hazer targets the growing market of graphite for batteries but also looks at integration into steel making, with hydrogen as an iron ore reductant and graphite as a co-reductant and “carburiser” for steel production (steel distinguishes itself from iron by a small proportion of carbon). As reported on this website in January 2020, Hazer has won support from the Australian Renewable Energy Agency for developing a first commercial demonstration project in Munster, Western Australia, which will split biogas from sewage treatment into hydrogen and solid carbon. The production is set to start in 2021. The use of biogas would possibly make the technology carbon negative, justifying a greener turquoise colour (what about viridian or chestnut teal?).
Another technology family is that of molten metal baths, in which methane is “bulled”. At temperatures around 1000°C the splitting of methane can again be both thermal and catalytic. The metal alloy of choice today seems to be nickel-bismuth, allowing for 90 to 95% of methane conversion. A coalition of European companies around the Dutch research organisation TNO is actively working in this field with its “EMBER” technology characterised by “microbubbling”, which reduces reaction time and reactor volumes. Difficulties are traditionally the same as with catalytic thermal splitting regarding the quality of both co-products, hydrogen and solid carbon. Commercial scale demonstration can be expected by 2025.
Then come the plasma technologies. A plasma is a gas of ions (atoms with some electrons missing) and free electrons. In cold or “non-thermal” plasmas only the electrons have a high temperature. Methane splitting in cold plasma, studied at the Tomsk polytechnic Institute in Russia, may hold great efficiency promises but is still at laboratory stage. A start-up, Atlantic Hydrogen, developed the cold plasma technology from 2010 to 2015 in New-Brunswick (Canada) but filed for bankruptcy in 2015.
Thermal plasmas allowing extremely high temperatures (over 5000°C in the plasma core) represent the state of the art for the industry – the only one that has already been proved at commercial scale. The Karbomont Hydrogen Plasma Black Reactor (HPBR) plant was built near Montreal in 1997 by the Norwegian engineering company Kvaerner – now Aker Solutions – after decades of development with the research organisation Sintef in Trondheim, based on a plasma torch technology run on direct-current electricity. It also used a molten salt carbon scrubber chamber. The plant had a design capacity of 20,000 tons of solid carbon and about 6,000 tons of hydrogen per year, and the intent was to sell it on the North-American market of carbon black.
Carbon black – not to be confused with black carbon or soot – is a valuable nanostructured material with more than 97% carbon, composed of fine spherical particulates forming aggregates or agglomerates. It is an industrial product with a global market of ~15 million tons per year, used for tires and other rubber products, and inks for printers, at prices from $0.5 to $2 per kg. In value, this is the largest solid carbon market accessible to methane splitting technologies, which can unfortunately not be designed to deliver carbon fibres or diamonds. Carbon black is currently produced from fossil fuels – often oil residues – with incomplete combustion, which is a polluting process.
The Karbomont Plant had difficulties achieving the expected quality of carbon black and had to sell its carbon at a much lower price than expected, while the hydrogen was sold to a nearby refinery. After several years of unsuccessful attempts to improve the quality of the solid carbon, the plant was closed as it could not be made profitable.
The challenge has been taken up further now by the company Monolith Materials, resting on a slightly different technology also developed since the early 90s in Europe – at Mines Paris Tech on its Sophia-Antipolis site (near Nice) by Laurent Fulcheri and his research team. The process rests on a 3-phase alternative current-generated thermal plasma. Monolith Materials also partnered with Aker Solutions to build on lessons learned at Karbomont. It ran for four years a 2 MW pilot reactor, “Seaport,” at Redwood City in Silicon Valley. The company began building the first unit of the Olive Creek Plant near Hallam, Nebraska, in October 2016 and the plant was said to be operational by 2020.
For each technology, scaling-up is a challenge. The larger the reactor, the more energy efficient it is, because its volume increases as the 2/3 power of the surface of its envelope, which is the key site of heat losses. However, the precise control of the quality of carbon black produced, which requires controlling the aggregation and agglomeration processes, depends on the geometry of the reactor.
The production of hydrogen is easier to control. In a first step, the hydrogen produced at Olive Creek will be sold to the Nebraska Public Power District, the State’s largest electric utility, to replace an existing coal-fired boiler at its Sheldon Station plant in Hallam.
The co-production of carbon black and hydrogen is key to the profitability of this technology in the short term, as turquoise hydrogen is presently undervalued for its zero GHG emissions characteristics. The global market of carbon black would facilitate the production of 5 Mt turquoise hydrogen – about 7% of a global market of pure hydrogen of ~70 Mt/y. Going beyond will require other carbon markets or a higher valuation of low carbon hydrogen or both. One important market for hydrogen in Nebraska and neighbouring states is, of course, that of ammonia for fertilising crops.
Turquoise hydrogen and ammonia offer an interesting pathway in the transition from fossil fuels to renewables. Addressing climate change requires decarbonising not only the power sector but all end-use sectors (buildings, industry, transport), through material and energy efficiency, direct use of renewable heat and, most importantly, electrification. Electrification can be direct or indirect via the production of hydrogen and hydrogen rich fuels and feedstocks. Greenhouse gas emissions should peak as soon as possible (or, could we say now, never return to pre-Covid-19 levels) and achieve net zero in the second half of the century. Achieving this will require a deployment of renewable energy capacities much faster than we currently see. Turquoise hydrogen can help speed up this process and provide us with very low carbon ammonia.
A guest article by Cédric Philibert, independent consultant and former Senior Analyst at the International Energy Agency.