China: scaling-up “flexible” ammonia production powered by renewable energy
By Kevin Rouwenhorst on June 28, 2023
In our May episode of Ammonia Project Features, Per Aggerholm Sørensen (Topsoe), Lili Lu (Envision), and Carol Xiao (ISPT) discussed renewable ammonia projects in China, with emphasis on scaling flexible ammonia production from pilot plants to gigawatt-size. The recording is available on the AEA’s Vimeo channel, and you can download the speaker presentations.
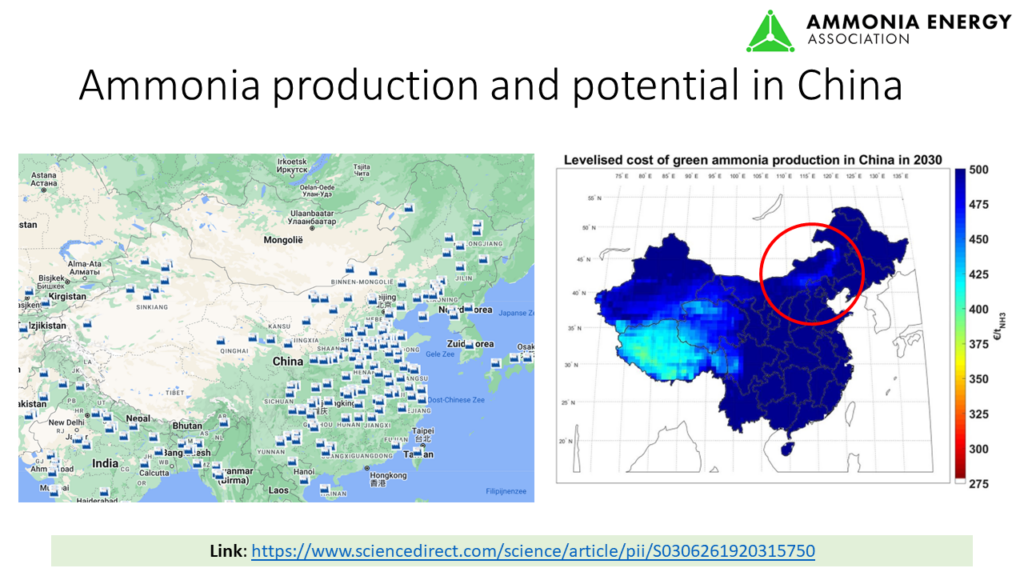
As of 2018, China had 54 million tonnes per year of ammonia production capacity, or about 25% of global ammonia production capacity. This is largely based on coal-based ammonia production, due to the absence of natural gas reserves in China. Coal-based ammonia production is among the most polluting pathways, with Scope 1 emissions amounting to at least 4 tonnes carbon dioxide emissions per tonne ammonia.
Typically, coal-based ammonia production is more expensive than natural gas-based ammonia production, especially in countries with low cost natural gas. Furthermore, China has an existing manufacturing base for electrolyzer production with gigawatt scale factories, at a cost substantially below that of western manufacturers. Lastly, an emission trading system was recently introduced in China. Given that China does not have substantial natural gas reserves, there is also very limited capacity for carbon capture and storage (CCS). This implies decarbonization needs to happen either via export of carbon dioxide via pipeline and ship, or more likely via electrolysis-based pathways coupled with renewables. The cost gap between fossil-based ammonia production and electrolysis-based ammonia production in China is arguably the smallest in the world.
According to Fasihi and coworkers, the regions with the lowest cost of renewable ammonia production in China are the western deserts, and the country’s northeast. Most of China’s current ammonia production and demand is located in the northeast, and various renewable ammonia projects have already been announced in this area:
- The Da’an project (Jilin Electric Power Company): 180,000 tonnes per year, date unknown. Multiple electrolyzer suppliers.
- The Baotou project (Mintal Hydrogen): 390,000 tonnes per year in 2025. Topsoe is the licensor of the flexible ammonia plant.
- The Chifeng project (Envision): 20,000 tonnes per year pilot plant in 2023 (Phase 0), 300,000 tonnes per year in 2024 (Phase 1), 300,000 tonnes per year in 2026 (Phase 2), and 900,000 tonnes per year in 2029 (Phase 3).
Two of these were the focus of discussion between our panelists.
Topsoe’s flexible ammonia technology: deploying & scaling
Topsoe is among the largest ammonia synthesis technology licensors globally, as well as an ammonia synthesis catalyst manufacturer. The Danish company is also making significant steps toward flexible ammonia technology, through a commercial-scale demonstration plant with subsequent scale-up to the world-scale.
Flexible ammonia technology is required to account for intermittency of renewables. As renewables typically account for considerably more than half of the total investment of a renewable ammonia plant, the downstream flexible ammonia plant should be “accommodating” towards renewable energy. Flexible ammonia production allows the plant to follow the generating output of renewable energy assets, thereby eliminating costly pressurized hydrogen storage, as previously discussed at Ammonia Energy.
Topsoe is demonstrating its flexible ammonia technology in the “Renewable Dynamic Distributed Ammonia Plant” (REDDAP) project in Lemvig, Denmark. The plant consists of 10 MW alkaline electrolyzer capacity supplied by Nel, coupled with 12 MW Vestas wind turbines and 50 MW solar PV capacity. The 25 tonnes per day ammonia plant is scheduled to start operation in the first half of 2024, with construction currently ongoing. A dynamic plant load in the range of 10-100% and a ramp rate of at least 3% per minute is currently claimed, but further flexibility enhancements may be realized with the demonstration plant.
The demonstration plant has been designed with the same type of equipment as large industrial plants, in order to allow for translating learnings from the demonstration plant to a commercial-scale operation. The demonstration plant has not been cost optimized because the equipment used for large scale plants is more costly at small scale. Furthermore, the demonstration plant utilizes the same control philosophy and instrumentation as a commercial scale plant.
Topsoe will scale up its dynamic ammonia plant to 1,800 tonnes per day ammonia production capacity in Baotou, Inner Mongolia, totalling 390,000 tonnes of ammonia production per year. The peak capacity in Baotou will be about half of the largest single train ammonia plant in the world. The plant will be directly coupled to renewable power from onshore wind. Basic engineering is ongoing, with production scheduled to start in 2025.
Further scale up of Topsoes flexible ammonia technology beyond the size of the largest operational fossil plants is already planned for NEOM, which is set to have a peak capacity of around 5,000 tonnes per day. Thus, by 2026-2027, Topsoe’s flexible ammonia technology will be demonstrated at full scale.
Envision Group: Chifeng
Inner Mongolia currently relies heavily on coal for its industrial activities. However, it is also an area with substantial potential for the development of onshore wind energy. In this context, Envision is developing flexible renewable ammonia production capacity near Chifeng city. The multiphase project has a total capacity of 1.5 million tonnes of ammonia per year. Phase 0 will be a pilot plant with 20,000 tonnes per year capacity, which is currently under construction and will be operational by September 2023. This is a scale-up by more than an order of magnitude compared to the largest flexible ammonia plant currently operating in Rajasthan, India.
Phase 1 is also under construction, with operations planned to start by December 2024, producing 300,000 tonnes of ammonia per year. Later phases are planned for 2026 (an additional 300,000 tonnes per year), and 2029 (an additional 900,000 tonnes per year) – if the market for zero-carbon ammonia develops sufficiently.
Ammonia produced by the pilot plant will be used in the domestic Chinese market. Ammonia produced from the first phase will be used for applications in the international market, with offtake currently under discussion. To accommodate this, ammonia storage & handling capacity will be developed by Envision in the port of Jinzhou City by the end of 2024, allowing for the berthing and loading of 100,000 DWT vessels.
The purpose of the pilot plant is to validate flexible ammonia production, explore the use of digital solutions in plant optimization, and assess the day-to-day operation of a flexible ammonia plant. This real-world data allows for optimization of the scale-up during the next phases of the project. The pilot plant will amount to nearly 100 tonnes per day of peak ammonia capacity, as well as 35 megawatts of combined alkaline electrolysis and PEM electrolysis capacity – bigger than any operational electrolysis facility for ammonia production.
The Chifeng project is Envision’s first announced renewable ammonia project, with multiple other locations currently under investigation. Envision is developing its own technology and market along the renewable ammonia value chain.
ISPT: the pathway to GW-scale
Scaling-up flexible ammonia production also implies a scale-up of electrolyzer capacity. ISPT has published reports on state-of-the-art designs for new 1 gigawatt alkaline and PEM electrolyzer plants. A 1 GW electrolyzer at full load produces about 150,000 tonnes of hydrogen per year. For reference, the Dutch industry currently requires 1.5 million tonnes of hydrogen per annum, which is equivalent to 10 GW of electrolysis capacity.
The state-of-the-art design for an alkaline electrolysis plant requires an area of 17 hectares, which can be optimized to 10 hectares. Building a 1 GW electrolyzer plant is not just a matter of numbering up stacks – optimizations to the balance of plant are required for scale-up. Interestingly, the electrolyzer stacks only represent a minor portion of the total plot area and costs (<20%). ISPT estimates that the installed cost of a 1 GW alkaline electrolysis system was about €1400 per kW in 2020, which reduces to €730 per kW in 2030, all based on western technologies. According to BloombergNEF, Chinese alkaline electrolysis systems are already available at a cost as low as $343 per kW, compared to $1200 per kW in Europe and North America.
ISPT is also involved in the MegaWatt Test Centre, wherein the performance of multiple megawatts of alkaline electrolyzers and PEM electrolyzers will be tested for dynamic operation. This is important, because oxygen and hydrogen gas cross-over may occur at reduced loads if the electrolyzers are not properly managed, causing an unsafe situation. Such learnings can be applied for future, scaled-up electrolyzer plants for safe operation.