Electrified Methane Reforming Could Reduce Ammonia’s CO2 Footprint
By Kevin Rouwenhorst on August 15, 2019
A May 2019 paper published in Science reports on a technological advance that may have significant implications for ammonia production. The paper, “Electrified methane reforming: A compact approach to greener industrial hydrogen production,” presents a method for providing the heat required for the highly endothermic steam methane reforming step from renewable electricity instead of natural gas. The carbon intensity of ammonia production could thereby be reduced by about 30%.
Other sources of hydrogen with a reduced carbon footprint previously described in Ammonia Energy reports include hydrogen from electrolysis of water, byproduct hydrogen, and conventional technology with carbon capture and sequestration.
Electrified methane reforming
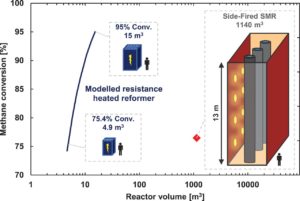
The paper’s nine authors, all of whom have Danish affiliations (including three who are employed by Ammonia Energy Association member Haldor Topsøe), propose to partially replace the natural gas used in conventional steam methane reforming with electricity: “eSMR” in Haldor Topsøe’s terminology.
The authors state that the cost-efficient scale of the electrified system could potentially be as much as two orders of magnitude smaller than a conventional SMR unit, due to the intensified contact between the ohmic heater and the catalyst layer. Among other benefits, this would allow downsizing of the colossal gas-fired SMR unit that typically occupies a major portion of an ammonia plant’s footprint. This would support the economics of small-scale ammonia plants.
Using electricity as a source of energy in ammonia production is not a new idea, but selecting high-cost electricity over low-cost methane clearly would not make economic sense. This reality was clear by 1928 when a contemporary author considered the question in a book on ammonia production:
Although electrolytic hydrogen is ideal for ammonia synthesis because of its purity it accounts for only 15 per cent of the ammonia produced by the direct synthetic ammonia process [the Haber-Bosch process]. The capital cost of a plant for the electrolysis is high, and except for a few especially favorable locations, electrical energy is more valuable for other industries.
Frank A. Ernst, Fixation of atmospheric nitrogen, Chapman & Hall, 1928.
The equation changes, though, when low-cost renewable electricity is available and a cost is levied on the emission of carbon dioxide.
A key feature of the electrified steam methane reformer is the thin catalyst layer on the wall of the reactor. Due to the highly endothermic nature of the SMR process, any active metal inside a thick catalyst pellet is not effectively used. Deploying catalyst in thin layers is beneficial for heat transfer and leads to a lower pressure drop in the reactor. The use of thin catalyst architecture in steam methane reforming has been advancing in recent years. For example, Johnson Matthey offers a “stackable structured reactor” in which thin catalyst layers are coated on cylindrical fin structures.
Impact on The Haber-Bosch process
While energy efficiency has been a key objective for Haber-Bosch technology developers over the past century, improving from 100 GJ per tonne in the 1920s down to 26-27 GJ per tonne for the best current technologies, carbon efficiency is the challenge of the 21st century. According to the International Fertilizer Association’s Energy Efficiency & CO2 Emissions benchmarking study in 2018, ammonia plants produce an average of 1.9 tonnes of CO2 per tonne of ammonia. (This number only includes natural gas-based ammonia plants; coal-based plants, and those using other heavy hydrocarbon feedstocks, emit far higher quantities of CO2.) The most energy efficient SMR-based ammonia synthesis plants produce around 1.6 tonnes of CO2 per tonne of ammonia.
The Science paper does not estimate the reduction in carbon emissions that the eSMR technology could support. (It includes only the statement that “Electrification of SMR offers a strong platform for new reactor design, scale, and implementation opportunities. Implemented on a global scale, this could correspond to a reduction of nearly 1% of all CO2 emissions.”) However, around 70% of the natural gas that enters a state-of-the-art ammonia plant is used as feedstock, reformed to provide hydrogen. The remainder is there to provide process heat, mainly in the reforming unit. It is this increment — approximately 30% of the natural gas consumption — that could be reduced or eliminated via the use of eSMR. In a state-of-the-art ammonia plant, producing 1.6 tonnes of CO2 per tonne of conventionally produced ammonia, this 30% reduction from electrified heating could result in a carbon intensity of 1.1 tonnes of CO2 per tonne of ammonia.
Low-cost solar and wind energy can be a driver for electrification of industry and reduced reliance on fossil fuels. The Science paper suggests that eSMR may prove economically viable in the coming decades in areas with abundant natural gas as well as low-cost solar and wind power. “The operating costs for an electrified reformer are directly related to the cost of electricity, natural gas, and CO2 taxes,” the authors say. “Preliminary estimates indicate that a resistance-heated reformer would be on par with current fired reformers in regions with a high production of renewable electricity.”
The paper also points to the role eSMR could play in supporting smaller-scale regional plants and in accommodating the variability of renewable electricity outputs:
With less need for heat recovery, resistance-heated reforming is efficient and applicable at many different sizes, promoting delocalization designs by using the existing and well-developed infrastructure of natural gas and potentially also biogas. Low thermal mass can also lead to reformers optimized for intermittent operation, following the fluctuations in availability of excess renewable energy with possible startup times in seconds.
S. Wismann et al., Electrified methane reforming: A compact approach to greener industrial hydrogen production, Science, May 24, 2019
It seems possible that eSMR technology could make a rapid transition from the laboratory to industrial use. At least that is the impression created by Haldor Topsøe’s announcement last month that it plans to build a demonstration plant in Denmark that will produce “CO2-neutral methanol from biogas using eSMR technology.” The plant is expected to be “fully operational in the beginning of 2022.”
Kevin Rouwenhorst is a Doctoral Candidate in the Catalytic Processes & Materials group at the University of Twente in the Netherlands.