MAN ammonia engine update
By Trevor Brown on January 30, 2020
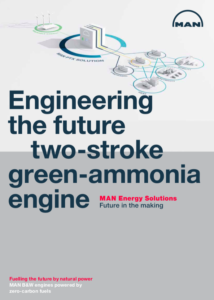
In November 2019, MAN ES published a technical paper describing the design and performance of its two-stroke green-ammonia engine. The paper also quietly announces the intentions of MAN ES to exploit ammonia energy technologies in a new business case, Power-to-X (PtX, “the carbon-neutral energy storage and sector coupling technology of the future”). In other words, MAN is moving into green ammonia fuel production.
In the two months since this paper was published, MAN’s ammonia engine has been central to a series of industrial collaborations that have been announced by shipbuilders and classification societies. As I reported last month, announcements made at the Marintec conference in China included plans for a 180,000 ton bulk carrier, a 2,700 TEU capacity Chittagongmax container carrier, and a 23,000 TEU Ultra-Large Container Ship, all fueled by ammonia.
Since those projects were announced, another collaboration with MAN ES has been announced by Lloyd’s Register, including MISC Berhad, and Samsung Heavy Industries (SHI), working together to develop “an ammonia tanker.”
Comparative fuel properties
MAN’s technical paper presents key data on maritime fuel properties. The argument for ammonia as an alternative fuel is clear when considering both energy density and CO2 emission reduction. The first impacts profitable cargo capacity, whereas the second impacts compliance, beyond today’s SOx and NOx regulations, with the IMO’s forthcoming GHG regulations.
Regarding energy density, if a conventional fuel tank (HFO) has a volume of 1,000 m3, an ammonia fuel tank would require 2,755 m3 to deliver the same power. This might make ammonia look infeasible if it weren’t for the apples-to-apples comparison against other carbon-free options: liquid hydrogen (at -253 °C) needing 4,117 m3, a Tesla model 3 battery requiring 14,000 m3, or the Corvus battery pack (the marine battery market leader) requiring 106,060 m3. Even carbon-based methanol offers no great advantage, requiring 2,333 m3.
Direct electrification (batteries) will always present the most energy efficient technology for providing power from renewables, and for short, quick journeys, battery-powered vessels will be ideal. For the long-haul, ocean-going freight, however, ammonia fuel offers an order of magnitude improvement on energy density, minimizing lost cargo space.
Regarding emission reductions, the various “low-carbon” fossil fuels — LNG, methanol, LPG — have the potential to reduce emissions relative to HFO between 5% and 18%. None of these have the potential to deliver anything close to the IMO’s 50% GHG emission reduction target. According to MAN’s data, however, ammonia fuel could deliver a 90% CO2 emission reduction.
The MAN ammonia engine
The MAN ammonia engine — although built to combust a fuel that is entirely new to the maritime industry — requires only a minor adaptation of an existing, mature technology.
The ME-LGIM engine type [which uses methanol as fuel] has been in service for some time and has achieved 50,000 running hours on methanol. The LGIM concept is used as basis for the LGIP engine [which uses LPG as fuel, and is now being adapted to use ammonia as fuel]. The development of the LGIM engine also dealt with some of the challenges related to ammonia, e.g. corrosion, toxicity and low flammability. The same engine concept, already verified at sea, will constitute the core of the ammonia-combusting engine. There will be no visible differences between an ammonia and an ME-LGIP/LGIM engine.
MAN ES technical paper, Engineering the future two-stroke green-ammonia engine, November 2019
The paper provides a brief history of research and development on ammonia engines, beginning in 1822, before summarizing the challenges of ammonia combustion and the benefits of its two-stroke combustion process.
The challenges related to ammonia combustion as concluded from research on combustion in smaller engines and turbines are the high NOX generation, low flammability and low radiation intensity. However, the benefits of the Diesel principle and the high combustion temperature of approximately 1300°C are a very stable and robust combustion. The typical dimensions and rpm of an MAN B&W two-stroke engine allow the time for a complete combustion of the fuel to take place. The high injection pressure enabling a nearly complete distribution of fuel in the combustion chamber also ensures this. Furthermore, the injection of pilot oil enables control of the combustion process and provides measures like pulsed or extended ignition. The possibility also exists to achieve the optimal progress of the combustion by changing the pilot oil type, for example to dimethyl ether (DME) or H2.
MAN ES technical paper, Engineering the future two-stroke green-ammonia engine, November 2019
While engine test results have not yet been published, strict control of NOx, unburnt ammonia, and other emissions (including pollutants beyond GHGs) are prerequisites for the adoption of ammonia as a maritime fuel, and MAN ES is working hard to ensure its technology performs.
Currently, research is carried out together with a university in Japan to assess the combustion and heat release characteristics of ammonia. The results of this research will guide the development of the specific fuel injection properties. However, it has been established that the supply pressure will be approximately 70 bar and the injection pressure 600 to 700 bar.
MAN ES technical paper, Engineering the future two-stroke green-ammonia engine, November 2019
Safety first: experience, double-walls, ventilation
As reflected in the collaborations between MAN ES and classification societies, which are the agents ultimately responsible for writing the rules that govern acceptable risks in ammonia fueled systems, safety is an integral part of design.
To quote only half a paragraph here:
Since ammonia is a toxic chemical, the proper safety precautions must be observed. However, on many vessels ammonia has been handled routinely as part of the SCR system. Note, that when comparing with previous applications of ammonia on shore, there are system differences. One is the already well-known double-walled design of fuel pipes. The fuel pipes on the ammonia engine are double walled and the design of the outer shielding pipe prevents gas outflow to machinery spaces in the event of a leakage or rupture of the inner gas pipe. A separate mechanical ventilation system with a capacity of 30 air changes per hour vents the intervening gas pipe space, including the space around valves, flanges, etc. Any leaking gas is led to the ventilated part of the pipe system, where hydrocarbon sensors will detect it.
MAN ES technical paper, Engineering the future two-stroke green-ammonia engine, November 2019
From maritime engines, to fuel production
This paper quietly announces MAN ES’s commercial interest in a new business case related to ammonia energy, beyond its ammonia engine.
The “MAN Energy Solutions Power to X (PtX) solution” proposes to manufacture green ammonia fuel. Electrolyzers, consuming renewable power and water, will produce green hydrogen that can be combined with atmospheric nitrogen in a Haber-Bosch plant, to synthesize green ammonia.
Power-to-X denotes the energy transformation from electricity to carbon-neutral synthetic fuels (gas or liquid) which can be stored and later used, like green ammonia.
MAN ES technical paper, Engineering the future two-stroke green-ammonia engine, November 2019
The inclusion of green ammonia as a PtX product is a welcome development for MAN ES. This is, in fact, such a new development that it is yet to be reflected anywhere else on the MAN ES website, including its Power-to-X Factsheet, which focuses exclusively on carbon-based fuels (methanol, eLNG), and omits nitrogen-based fuels (ammonia) and hydrogen itself. As PtX proponents gain a better understanding of the fuel properties that will be compliant with future IMO regulations, we can expect ammonia to become the increasingly mainstream PtX product.