Renewable ammonia in China: full speed ahead
By Kevin Rouwenhorst on February 28, 2024
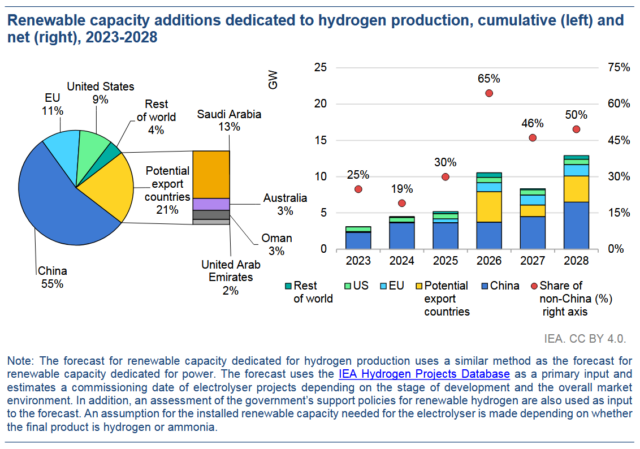
Click to expand. Renewable capacity additions for hydrogen production by 2028. From Renewables 2023: Analysis and forecast to 2028 (IEA, Jan 2024).
This month, the International Energy Agency (IEA) released its Renewables 2023 Report. The report found that many electrolysis-based hydrogen and ammonia projects have been announced, but the projected installed electrolysis capacity in 2028 has decreased substantially since last year’s edition of the report. But while this trend is true for most global regions, China’s projected capacity has in fact stayed the same. China is expected to represent 55% of the installed 45 GW of renewable generating capacity for hydrogen by 2028, according to the IEA.
Assuming about 2-3 GW of renewable generating capacity per million tonnes of ammonia renewable production, this could result in 4-6 million tonnes of renewable ammonia in China by 2028. This is equivalent to 7-10% of current ammonia demand in China (see below).
From coal to renewable energy
China is the largest ammonia producer globally, and the country accounts for almost 32% of total global demand. Ammonia is produced from fossil gas in most countries, but this is not abundant in China. Thus, about 85% of China’s annual ammonia production is based on coal. The carbon intensity of coal-based ammonia production is substantial, with at least 3.5-4.5 tonnes CO2 equivalents emitted per tonne ammonia. This makes China one of the largest emitters in the ammonia industry today.
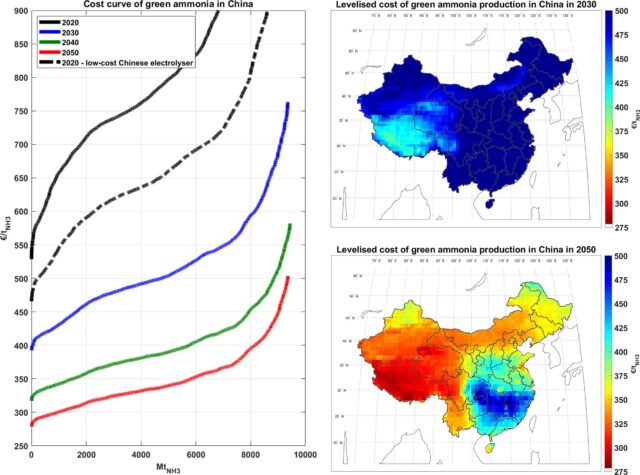
Click to expand. Wind energy profiles in China, reproduced from the Global Wind Atlas.
However, this is expected to change very soon. Renewable ammonia exports from the Inner Mongolia Autonomous Region – one of the areas with most onshore wind potential China – could begin this year. In fact, the first pilot plant of Envision located in Inner Mongolia’s Chifeng City is currently being commissioned, with a capacity of 20,000 tonnes per year. On average, the estimated investment cost of the various projects in Inner Mongolia is just shy of USD 5000 per tonne. For reference, the total investment for NEOM is USD 8.4 billion USD for a 1.2 million tonnes plant (or USD 7000 per tonne).
So, why is China scaling its renewable ammonia capacity substantially faster than most countries? First of all, there is a smaller cost difference between coal-based ammonia production and renewable ammonia there (compared to gas-based ammonia vs. renewable ammonia production in other countries). Coal-based ammonia production is estimated to cost around USD 380-410 per tonne, not accounting for carbon emission taxation. By 2030, researchers estimate that renewable ammonia can be produced at a cost of USD 400-500 per tonne in various regions.
China has built its own manufacturing ecosystem to support this transition. Not only does China produce components for renewable energy generation, but Chinese-made electrolyzers are substantially cheaper than western electrolyzers. Deployed ammonia synthesis technology in China is a mixture of western technology (such as Topsoe’s in Baotou), and domestic technology.
Permitting and state funding of projects proceeds at an accelerated rate in China. The Chinese government mandates the replacement of inefficient operational capacity by state-of-the art technology, resulting in shorter lifetimes for industrial plant. Typical assets in the power and heavy industry in China have a 25-35 years lifetime, while globally this is 30-50 years.
Finally, we note that coal-based ammonia plants have a relatively high capital intensity, and especially in this case, as typical Chinese ammonia plants are smaller-sized. This helps bridge the gap to the capital intensity of renewable ammonia. Considering also that future increases in the Chinese ETS (emission trading system) will occur, newbuild coal-based ammonia capacity in China is simply not economical.
The intermittency challenge ahead
Click to enlarge. Sinopec’s Kuqa facility. The six large buildings with the red roof have 40 MW electrolysis capacity each, and the small building with the red roof has 20 MW electrolysis capacity installed. In the rear, hydrogen storage spheres are installed. Source: Sinopec.
China has already installed its first multi-hundred MW projects. The largest installed electrolyzer plant is Sinopec’s Kuqa facility in Xinjiang, which has 260 MW of alkaline electrolysis capacity. As recently reported, this plant faces issues with flexible operation of the electrolyzers, which rely on power generated by an adjacent solar PV plant. Sustained, long-term operation of electrolyzers at lower-than-nameplate capacities is a serious challenge that requires further optimization. Operational experience gained at Chinese projects over the next year or so will be invaluable to solving this challenge.