Ammonia fuel for industrial ceramics manufacturing
By Kevin Rouwenhorst on May 02, 2025
In our April Episode of Project Features, Professor Yi-Bing Cheng from Foshan Xianhu Laboratory, and Qikang Zhang and Chuyun Zhang from Monalisa Group explored a recent demonstration of ammonia combustion for industrial fabrication of ceramic tiles in China. The recording is available on the AEA’s website, and you can also download the speaker presentations.
Ammonia for heat: evolving industrial applications
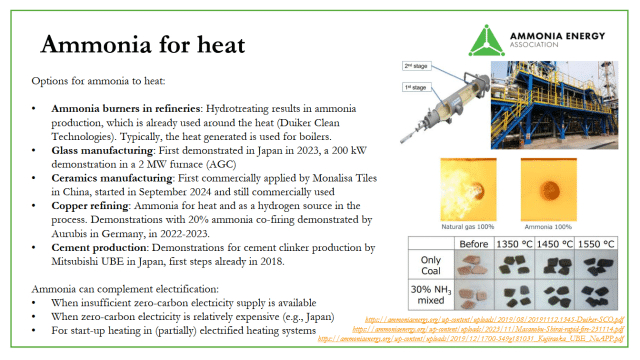
Click to expand. Summary of ammonia for heat applications to date. From Kevin Rouwenhorst, April 2025 Project Features introduction.
Ammonia is a zero-carbon fuel that can be used for high temperature heat applications. To date, various ammonia to heat applications have been demonstrated, such as in commercial glass furnaces (AGC in Japan), for copper wire production (Aurubis in Germany), for cement clinker production (Heidelberg Materials in the UK; Mitsubishi UBE in Japan), and of course ceramic tile manufacturing (Monalisa Group and Foshan Xianhu Laboratory in China). Ammonia-rich fuel mixtures are also sometimes combusted for heat in the hydro treating section of refineries (Duiker Clean Technologies). Other possible applications include aluminum smelting and steel making. Electrification with renewable power for heating is another possible solution, but will be dependent on a range of factors, including reliable availability of low-cost renewable electrons.
Ceramics production with ammonia burners in Foshan
The ceramics industry in the Chinese city of Foshan in the province Guangdong accounts for about 10% of China’s ceramic production. Foshan’s ceramics industry had an output value of 102 billion Yuan (14 billion USD) in 2023, around 7% of the city’s GDP. The ceramics industry also accounts for about 30% of total CO2 emissions in Foshan, with 30% of emissions from electricity and raw materials, and 70% from combustion during the baking process.
To fully displace fossil fuels, around 3.5 million tons of ammonia per year would be required to decarbonize in Foshan’s ceramics industry, and about 8.1 million tons for the whole of Guangdong province. To decarbonize the entire Chinese ceramics industry, about 35 million tons of ammonia would be required every year. This represents a significant demand potential for ammonia fuel in China, at a local, national and multi-sector level.
Pilot ceramics fabrication line
Click to expand. Pilot ceramic roller kiln retrofitted with ammonia burners. From Yi-Bing Cheng, Ammonia Combustion for Industrial Fabrication of Ceramic Tiles in China (Apr 2025).
Foshan Xianhu Laboratory has various pilot-scale furnaces for heat applications, allowing for testing zero-carbon fuels like ammonia and hydrogen, sometimes blended with natural gas or coal powder. Following initial research, Foshan Xianhu Laboratory joined forces with Foshan Oceano Ceramics and Foshan DLT Technology in 2021, to convert Oceano’s pilot ceramics fabrication line from natural gas to ammonia fuel. The 30 meters long pilot ceramics fabrication line (100,000 m2/year capacity) was retrofitted from natural gas burners to ammonia burners, with 18 burners on each side (36 in total) for heating to about 1250°C. On the 18th of December 2022, the first ammonia-fueled ceramic tile was produced. A detailed scientific account of this pilot can be found in a recent research paper published in Energy & Fuels.
Click to expand. Ammonia swirl burners designed for stable ignition, stable combustion, and emissions control. From Yi-Bing Cheng, Ammonia Combustion for Industrial Fabrication of Ceramic Tiles in China (Apr 2025).
Controllable ignition of ammonia was a technical challenge, owing to ammonia’s high ignition energy. Also, maintaining a controllable and stable high temperature flame was a technical challenge, owing to ammonia’s low flame speed and narrow flammability limit. Swirl burners were designed specifically for stable ammonia ignition and combustion, limiting the nitrogen oxides (NOX) emissions and ammonia slip. Such burners can operate on ammonia, natural gas, or a mixture thereof.
Commercial-scale ceramics manufacturing using ammonia at Monalisa Group
Click to expand. Monalisa’s ammonia-fired ceramics manufacturing demonstration. From Qikang Zhang, World’s First Ammonia-Hudrogen Zero-Carbon Combustion Technology Demonstration Production Line for the Ceramics Industry (Apr 2025).
In late 2023, ceramics manufacturer Monalisa Group and Foshan Xianhu Laboratory announced an ammonia for heat project for ceramic tiles manufacturing in Nanhai District of Foshan City, China. The Monalisa production line is 150 meters in length, with 300 burners, and 1,500,000 m2/y ceramic tiles production capacity. Retrofitting occurred between April and September 2024, while also constructing an ammonia fueling station, with two 15 ton ammonia storage tanks, an absorption tank, a vaporizer with a capacity of 1.2 tons per hour, and a buffer tank. The CO2 mitigation from the ceramics manufacturing line is about 5,200 tons per year, upon using pure ammonia as fuel.
Regulations for the design, material selection, installation, and operations already exist for ammonia storage, piping and valves. However, such regulations did not exist for industrial ammonia combustion in ceramics manufacturing. Foshan Xianhu Laboratory and the Guangdong Ceramic Society drafted a “Code for application of ammonia fuel in ceramic industry”, which has been endorsed by an expert panel and is within the National Standard Management Committee for recording in China. The code includes health and safety regulations, as well as training. There have been no safety issues so far. As the presenters explained, ammonia safety throughout the whole demonstration project was manageable and controllable – a promising indicator for rollout of the technology to other production lines.
Ammonia was first introduced in the firing process during tile manufacturing in September 2024, and the operation was a huge success. Using ammonia as fuel did not compromise the color and quality of the produced ceramic tiles, which passed quality acceptance testing. As certified by a third party, NOX emissions were also well below acceptable thresholds, thanks to some unique mitigation strategies.
Emissions mitigation: “mutli-level” DeNOX
Click to expand. Multi-level DeNOX approach to mitigate emissions from ammonia combustion in ceramics tile manufacturing. From Yi-Bing Cheng, Ammonia Combustion for Industrial Fabrication of Ceramic Tiles in China (Apr 2025).
Three strategies are used to minimize emissions from ammonia combustion, namely (1) using staged-burners, using a (2) Selective non-catalytic reduction (SNCR) for DeNOX, and (3) Selective catalytic reduction (SCR) for DeNOX. Emissions-wise, two-staged burners using ammonia fuel resulted in much reduced NOX emissions versus single-staged combustion, and nitrous oxide (N2O) emissions <5 ppm. NOX emissions are further mitigated to single-digit ppm levels using the two DeNOX technologies. The SNCR (Selective Non Catalytic Reduction) for DeNOX injects ammonia gas in the exhaust gas, to react with NOX at 850-1100°C in absence of a catalyst, to form water and atmospheric nitrogen. After the NSCR, an SCR (Selective Catalytic Reduction) step is used, where gaseous ammonia is injected to react with residual NOX, yielding NOX outlet concentrations of 10 ppm, well below the Chinese regulatory limit of 49 ppm.
Target markets, next steps
With the successful commercial demonstration in Foshan, Monalisa Group has its sights set on EU markets for its decarbonized ceramic tiles, as well as domestic sales. Moving quickly to be the first onto a new market is a priority. With EU policy leading the way for decarbonized industrial products, the presenters hope that China’s government will lift ambitions and implement stronger policy to encourage solutions like ammonia-fueled ceramic tile manufacturing. In 5-10 years’ time, further rollout of the ammonia-fueled production lines across other Monalia facilities is anticipated, along with the hope of expanding deployment into other high-temperature industries. The strategic pattern employed in Foshan – demonstrate success/feasibility, promote, then deploy – can be applied elsewhere in China, driving decarbonization across a range of industries.