3rd generation ammonia synthesis: new catalysts & production pathways
By Julian Atchison on December 08, 2021
New ruthenium hydride catalyst for mild condition synthesis
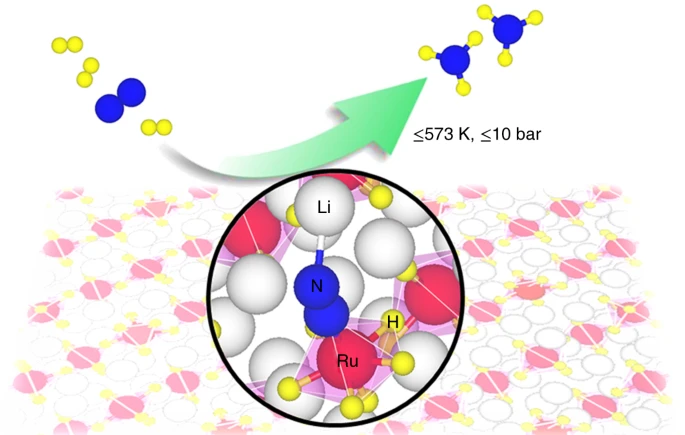
A team from DTU Energy and the Dalian Institute of Chemical Physics have uncovered a new class of alternative catalysts for mild condition ammonia synthesis. The ternary ruthenium complex hydrides Li4RuH6 and Ba2RuH6 avoid the energy-intensive pathway of nitrogen dissociation in a “synergistic” manner. The electron and proton-rich [RuH6] centers anchor the nitrogen molecules, while hydrogen molecules (H2) transport electrons and protons between them. Li and Ba stabilise various intermediate species as ammonia forms – without the nitrogen molecule having to be forced apart for the reaction to occur. Ammonia synthesis occurred at temperatures as low as 300°C and at pressures as low as 1 bar.
Professor Tejs Vegge from DTU Energy remarked: “Everything is different from what we’ve seen before…You could picture this catalyst as a symphony orchestra, where every part has to function together to make it work. The fascinating part is that it does work – there are no false notes…it may also open up new possibilities for ammonia production to take place in a less energy-intensive way.”
New process for plasma synthesis
A team from the Korea Institute of Machinery and Materials has reported a highly selective plasma ammonia synthesis method. H2 and nitric oxides (NOx) are co-generated in a single step once water is added to nitrogen plasma, with 99% of NOx produced in in the form of NO. Nitrogen monoxide then reacts with H2 to form ammonia with 95% selectivity. The researchers report this system results in an ammonia concentration of ∼0.84% and a production rate of 120 μmol/s. A by-product aqueous nitrate solution can be utilised for agriculture, or as an oxidising agent.
The next step for the team? Scaling up, commercialising and finding new collaborators…as is always the case with 3rd generation synthesis R&D!
New electrode for direct electrochemical nitrogen reduction
And a team from Delft University of Technology has presented an present an “unconventional electrochemical design” that physically separates electrolytic hydrogen activation from catalytic dinitrogen activation & hydrogenation by a dense – but permeable – metallic electrode (thin nickel foil was used for this experiment).
In ambient conditions, water reacts in the electrolytic compartment to produce atomic hydrogen (ie. protons) that permeate through the Ni-based metallic layer towards the gaseous compartment. On the gaseous side of the electrode, dinitrogen adsorbs to the surface and reacts with the permeated atomic hydrogen to produce ammonia. The authors demonstrate that dinitrogen is activated via the Mars–van Krevelen mechanism (a phenomenon also observed in a recent cracking breakthrough), and that the presence of active nitrogen on the electrode surface then hinders the activation of gaseous H2 (ie. the conventional method of ammonia synthesis). All of this adds up to demonstrate a truly novel mechanism for direct electrolytic ammonia production at ambient conditions.
Mechanochemical ammonia
A team at the Max Planck Institute for Coal Research has demonstrated a new mechanochemical ammonia synthesis system that operates at room temperature and pressures as low as 1 bar. R&D into mechanochemical synthesis methods has been active for around fifty years, and revolves around a basic principle: a reactor mills (or smashes!) together steel balls, gaseous nitrogen, hydrogen and a solid-phase iron catalyst to produce ammonia. But yields have been historically low, and until recently the process hasn’t been considered “continuous” or “looping” like Haber Bosch.
Here, the authors follow on from a recent discovery that lower-temperature chemical looping can produce mechanochemical ammonia in a semi-continuous fashion. Their catalyst was powdered iron with small amounts of elemental Cs, and the system functioned both under batch and continuous conditions for 60 hours, producing gaseous ammonia at values up to 0.42 vol%. Further work is needed to improve yields to the level of a two-step, elevated temperature-and-pressure, batch mechanochemical process published last year – as high as 90% ammonia in the output gas. Combining the two breakthroughs – continuous operation and high yield – will be key to realising commercialisation of mechanochemical ammonia. Proponents believe it represents a new pathway forward for distributed and point-of-use fertiliser production.