R&D recap: the Journal of Ammonia Energy
By Geofrey Njovu on August 06, 2024
The Symposium on Ammonia Energy in Shanghai next month will assemble experts from industry and academia to discuss the way forward for ammonia as an energy vector and a low-carbon fuel for the future.
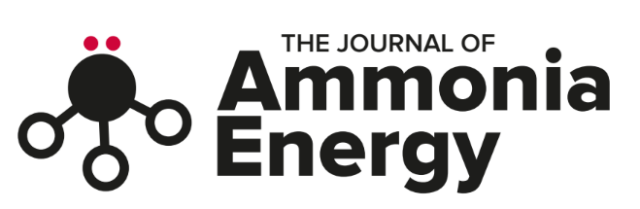
In association with the annual symposium, the open-access Journal of Ammonia Energy brings together the research and key findings presented at the event, with the first two editions (Cardiff in 2022 and Orleans in 2023) now available.
Published in association with the annual symposium, the open-access Journal of Ammonia Energy serves as a platform for ammonia research, ranging from combustion engineering, cracking catalyst design, exhaust emissions control, and health and safety controls (amongst others). The first volume collates research that was presented at the first symposium, held at Cardiff University in September 2022.
Early-bird registration is still open for the Shanghai event, which will be held from September 22-26. But before Shanghai, we will take this opportunity to highlight select papers and key results from the first two volumes of the journal, starting with Cardiff (2022). Volume I can be accessed in full here.
Volume I theme: overcoming combustion challenges
Much of the research in the first volume focused on overcoming the difficult properties of ammonia fuel, including its low reactivity, unstable flame regimes, low laminar burning velocity, NOX emissions, and high auto-ignition temperature. Compared to hydrocarbon fuels, this presents different engineering, chemistry, environmental, and health and safety challenges. Approaches such as ammonia blending with other fuels (eg. hydrogen or diesel), assisted ignition, and innovative combustor design can help mitigate some of the challenges associated with the use of ammonia fuel.
The volume concludes with a succinct report on the health & safety session that was held at the Cardiff symposium. The report lays out various questions posed by different stakeholders during the discussion, plus a set of recommendations such as establishing cross-cutting standards and regulations covering both suppliers and consumers.
Minimising diesel pilot fuel “not necessarily the best strategy”
Click to enlarge. The experimental setup used in this study to assess the variation of the exhaust composition when ammonia is used as a dual fuel with a small fraction of diesel. From Dupuy et al., “Experimental Study of RCCI (Reactivity Controlled Combustion Ignition) engine – ammonia combustion with diesel pilot injection”, Journal of Ammonia Energy 1 (2023).
Due to its low reactivity and high auto-ignition temperature, ammonia is often blended with other fuels to enhance combustion performance and stability. In this paper, a small fraction of diesel is added to ammonia fuel in a “Reactivity Controlled Combustion Ignition” (RCCI) engine, and the corresponding exhaust emissions are characterised. Particular attention is given to N2O, which has a global warming potential of over 250 times greater than that of CO2 at equivalent mass. The fraction of diesel used in the study goes up to 12.5% Diesel Energy Fraction (DEF) and its impact on the performance and emissions in a single cylinder 0.5L engine.
The work, a collaboration between the University of Orleans and engine manufacturer WinGD, demonstrates that lowering the diesel fraction “might not be necessarily the best strategy to minimise carbon footprint”, as the trade-off is higher N2O emissions. The authors also found that combustion duration and the average in-cylinder temperature are two key indicators of N2O levels at the exhaust.
Obtaining the optimal fuel blend via cracking
Click to enlarge. The proposed reaction scheme of ammonia cracking using a transition metal – promoted lithium amide catalyst. From Brooker-Davis et al., “Enhancement of the catalytic activity of lithium amide towards ammonia decomposition by addition of transition metals”, Journal of Ammonia Energy 1 (2023).
Still on ammonia fuel blending, this paper sought to explain the reaction mechanism of a promoted lithium nitride catalyst used for ammonia decomposition, or cracking. NH3/H2 blends are typically achieved by catalytically cracking a proportion of the starting ammonia to hydrogen. As the ratio of NH3/H2 is crucial in the combustion performance and the composition of exhaust gases, it is important to fully understand the mechanism of ammonia cracking. In this work, it is stated that, in the case of retrofitting current ICE engines to run on ammonia, a partial cracking of ammonia to release about 4-5 wt% of hydrogen is required to improve flame properties and combustion.
By conducting ammonia decomposition experiments and gravimetric studies, the authors showed that, at elevated temperatures, the lithium amide undergoes a phase transformation to form an imide-rich phase which enhances catalytic activity. They also demonstrated that promoting the catalyst with Cr or Mn reduces the formation temperature of the imide-rich phase, increasing energy efficiency. The mechanism of ammonia decomposition of the catalyst is schematically displayed to the right.
Increase swirl intensity, reduce NOX emissions
Click to enlarge. The adjustable axial swirler. From Wang et al., “Exploring the Effects of Swirl Intensity on NO Emission in Ammonia-Methane-Air Premixed Swirling Flames”, Journal of Ammonia Energy 1 (2023).
Among other factors, “swirl intensity” affects NOX emissions in ammonia fuel exhausts.
In this paper, an adjustable axial swirler capable of high swirl numbers (pictured to the left) was designed, built and tested to study the impact of swirl intensity on NOX emissions. The study focused on flame swirl from a premixed ammonia-methane-air fuel mixture. Higher swirl intensities (indicated by a higher “swirl number”) require a more complex combustor design.
The research found that increasing the swirl number from 0.6 to 1.0 resulted in a more compact flame, with enhanced reactions in the corner recirculation zone. It also demonstrated that varying the swirl number significantly alters the NO concentration in the exhaust gas. NO concentration was “significantly reduced at an equivalence ratio of 0.90 and an ammonia fraction greater than 80%”.
At higher swirl intensities, more heat is lost to the combustor wall which reduces the flame temperature in the main reaction zone. This in turn inhibits the formation of OH radicals, and consequently results in low NO emissions. Optimising the swirl intensity via combustor design can therefore be an effective way to stabilise ammonia combustion, thereby reducing NOX emissions.
Spark-assisted compression ignition of ammonia comparable to gasoline
Click to enlarge. Experimental set up of the SACI study of pure NH3 and NH3/H2 fuel. From Reggeti et al., “Experimental Investigation of Spark-Assisted Compression-Ignition with Ammonia-Hydrogen Blends”, Journal of Ammonia Energy 1 (2023).
This paper investigated the ammonia fuel performance in a spark-assisted compression ignition (SACI) engine. This ignition mode has been proposed for enhancing ammonia ignition, given its high ignition energy and slow flame speed. The high octane rating of ammonia allows for a high compression ratio, which is necessary for SACI engines.
A high compression ratio CFR engine was tested on 100% NH3 or with NH3/H2 blend with 2.5 and 5% by volume of hydrogen. A wide range of intake temperatures and spark timings were used at two different engine speeds.
Among other findings, it was observed that small amounts of H2 blending “benefitted gross indicated mean effective pressure (gIMEP) at maximum brake torque (MBT), but pure NH3 was more stable across a wide range of spark timings and intake temperatures”. The combustion durations observed were comparable to gasoline-fuelled spark ignition engines, demonstrating that combustion via SACI compensated for NH3’s low flame speed.
In the exhaust, it was found that hydrogen blending and high intake temperature increased NO emissions. A clear relationship between hydrogen blending and N2O was not observed, but its concentration increased at higher engine speeds.
Ammonia’s unique health & safety challenges
Ammonia properties such as its toxicity, flammability and corrosiveness present unique challenges. This workshop session at the Cardiff symposium covered the health and safety issues that can arise from the production, handling, distribution and use of ammonia as an energy source, and potential mitigation strategies. Some of the key discussion points included:
- Compared to established industries, such as fertiliser manufacturing in which ammonia is handled by trained people, new uses of ammonia as an energy carrier and fuel may increase exposure risk to untrained end-users. Although this will require new strategies such as increased awareness campaigns, precedence from existing industries on safe handling is transferable. New entrants and incumbents should collaborate to exchange knowledge and devise solutions for new risks.
- The potential for decentralised production enabled by the availability of renewable energy should account for the potential end-user. Production systems should be made safer accounting for inexperienced handlers of the chemical. Additionally, comprehensive risk assessments, tests and demonstrations should be carried out before mass decentralised deployment.
- Exposure risks are particularly high at transfer points to tanks, the filling of cylinders, and especially for operations near populated areas. In addition to designing safer systems, interjurisdictional, industry-wide standards and regulations should be introduced, learning from other industries (including fossil fuels).
- To use ammonia in the marine industry, engine and vessel design will require adjusting to account for ammonia’s higher toxicity, high flashpoint as a fuel and increased danger to human and aquatic life, compared to conventional fuels. Considering these complications, it was suggested that “ammonia may ultimately prove to be a more appropriate solution for deep-sea cargo ships rather than short-sea, passenger or inland waterway craft.”